A strong, dependable supply chain is the backbone of your small or medium-sized enterprise, making it important to devote just as much attention to the supply side of your business as the sales side.
From automation to personal relationships, a variety of factors go into creating a supply chain that’s capable of driving your business to new heights. For many businesses, many aspects of supply chain management can be optimised, improved and built upon for better results.
Below, we’ve listed five tips to help you more effectively manage your SME’s supply chain, from eliminating delays and setbacks caused by human error to maximising the potential of each and every participant in the process.
Remember that relationships drive a strong supply chain
One of the most common SME supply chain management mistakes is forgetting that, at the end of the day, a huge aspect of building a strong supply chain is developing and maintaining great relationships with your suppliers.
From paying suppliers on time to reaching out to sales representatives and other staff, many of the small, everyday processes involved in maintaining the human side of your supply chain can play an important role in strengthening this side of your business.
Buying internationally? Understand the effects of foreign exchange rates
Are your SME’s suppliers located in other countries? If you buy goods or services from suppliers located in other countries, it’s important that you’re aware of the potential impact exchange rates could have on your business.
Exchange rates can fluctuate, often by a significant amount. In the post-Brexit world, where swift falls or gains in currency valuations aren’t uncommon, it’s important to stay on top of the risks a swing in foreign exchange values could have on your supply chain.
Make transparent, consistent and helpful communication a priority
Even small and mid-sized enterprises can have complicated supply chains that involve several layers of suppliers, contractors and subcontractors. As a result, it’s important to make focused, clear communication a priority as your supply chain grows more complex.
From remote conferences to phone calls, emails and other forms of communication, keeping in touch with people on every layer of your supply chain can give your business a major edge, as well as the ability to respond faster to disruptive events and opportunities.
Improve efficiency by reducing paperwork and human error
Many supply chain setbacks are the end result of human error, from late payments to data entry mistakes, lost documents and more. Because of this, one of the easiest ways to optimise your SME’s supply chain is by reducing the risk of human error affecting communications.
EDI platforms like XEDI, which allow customers to connect directly with their suppliers to make and process orders, are designed to help you automate large aspects of your order process to speed up the supply chain management process and limit room for human error.
Capitalise on your suppliers’ unique strengths and advantages
All too often, businesses view their suppliers as commodities — sources of a specific product or service — rather than as differentiated offerings. As a result, unique advantages that a supplier might offer go ignored rather than used to create better results.
One way to potentially improve your SME supply chain is by reaching out to suppliers to learn more about their specific resources and skill sets. You might be surprised to discover that your existing suppliers have additional skills and resources to take your project to the next level.
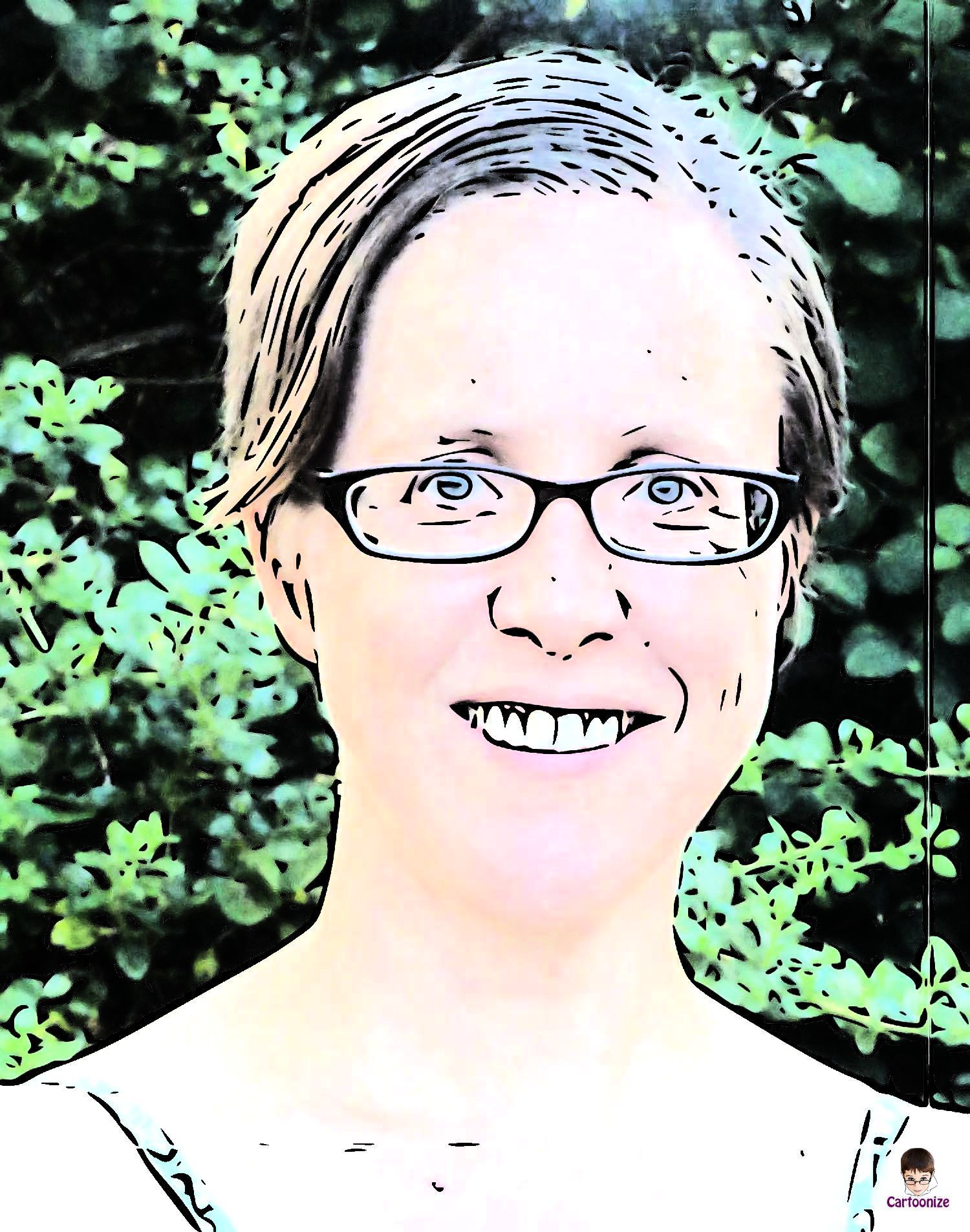
Jenny has been reporting on small business issues since 2001 where she held a number of freelance positions across the leading SME publications in the UK. Specialist subjects included SME financing and tax.