Software companies DUALIS GmbH IT Solution and iTAC Software AG have developed a holistic digitalization approach for greater efficiency, flexibility and quality in manufacturing. The approach is based around a ‘digital twin’ which uses simulation platform Visual Components to create a digital replica of an entire production line.
From the simulations, GANTTPLAN advanced planning and scheduling system (APS) from DUALIS is used to generate a model for realistic production planning. Data is then transferred to iTAC Software AG’s iTAC.MOM.Suite manufacturing operations management system to form an interface between production and IT systems.
The data from the MOM and APS systems is then sent back to the simulation in a closed loop approach for continuous optimization of the process flows. According to Alina Leber, of iTAC Software AG, this allows for “real-time monitoring of production processes and precise calculation of the future”.
The holistic digitalization approach developed by DUALIS GmbH IT Solution and iTAC Software AG offers businesses increased efficiency, flexibility and quality in manufacturing. With the capabilities of the digital twin, simulation, APS and MOM/MES systems, the approach promises to minimize costs and risks.
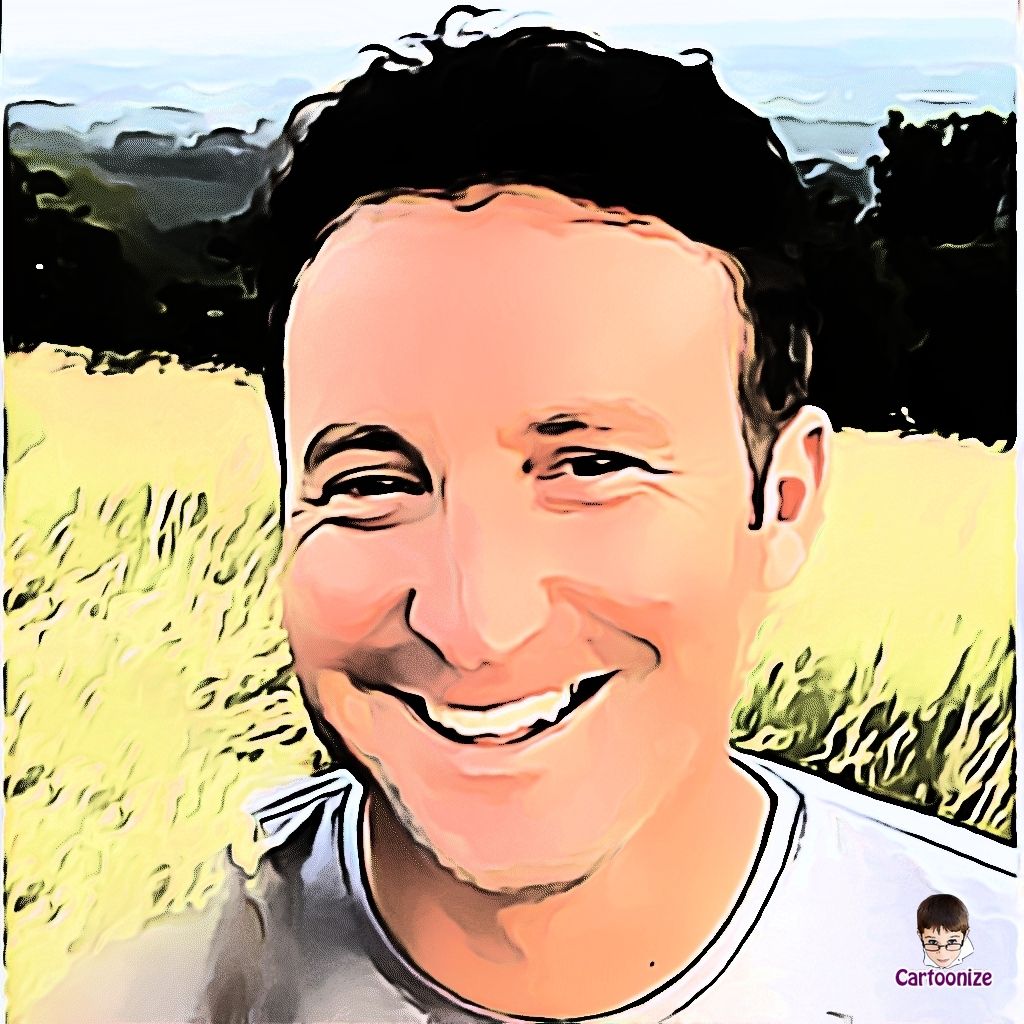
Derick is an experienced reporter having held multiple senior roles for large publishers across Europe. Specialist subjects include small business and financial emerging markets.